面向增材制造的新型换热器设计
案例概括
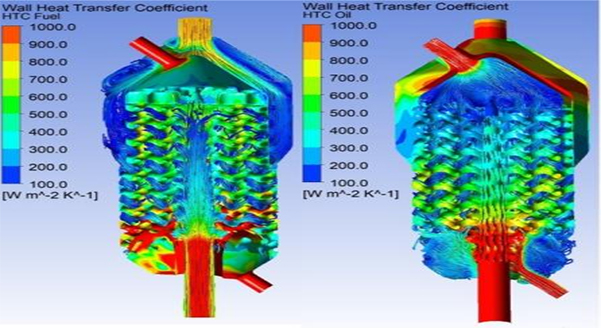
换热器做为提升发动机热管理水平的关键部件,紧凑高效的结构设计可以大大提升换热性能,基于增材制造技术所带来的自由度,使得复杂精细的三周期极小曲面TPMS胞元填充的换热器设计成为可能。本案例基于新一代面向增材制造的设计平台技术、CAE仿真技术、工艺仿真技术、工业CT扫描技术等,开展了面向增材制造的新型换热器的快速研发验证。
项目挑战
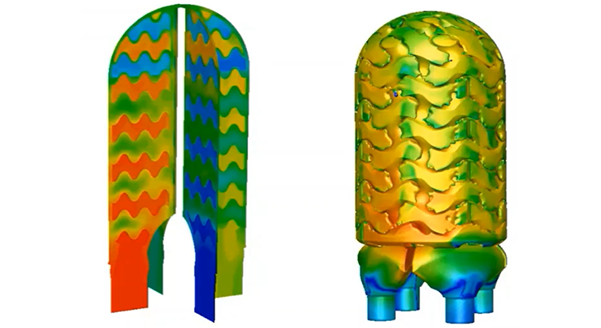
新型换热器采用力学性能优异、比表面积大、质量轻、具有天然的冷热双通道等优势的三周期极小曲面TPMS胞元填充,虽然结构紧凑度大大提高,换热性能提升,实现轻质高效,但给设计、仿真、制造、检测等环节均带来巨大挑战。复杂的TPMS单元空间周期排布设计,要求具备合适的设计工具,同时流体、结构仿真验证方法既要保证一定精度,又要快速验证;此外薄壁、高度空间周期排布的TPMS单元增材成形质量控制,以及尺寸、缺陷检测等都存在技术挑战。
解决方案
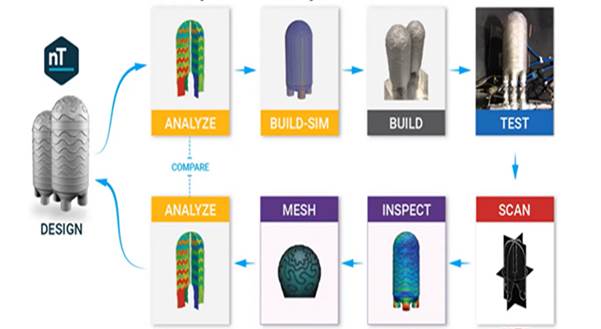
面向增材制造的新型换热器设计,解决方案如下:
1.采用新一代基于隐式建模技术的增材设计平台,进行TPMS胞元填充设计,大大提升设计效率;
2.基于CAE仿真平台,实现TPMS胞元填充换热器的快速流体、结构验证;
3.采用增材工艺仿真技术,提前预测换热器成形质量,优化设计结构、工艺方案,保证成形质量;
4.基于工业CT扫描技术,进行断层扫描,分析缺陷;
5.采用三维数据重建技术,实现打印模型的快速重建,并进行仿真验证,迭代优化。
用户价值
相比传统换热器,新型换热器体积减少85%,重量降低81%,总体热传导效率提升1.8倍,TPMS胞元热传导效率提升11.7倍,冷却测压降增加16%,燃气测降低9.1倍,胞元换热面积增加146%;新型换热器采用高强度铝合金增材制造,材料力学性能优异,制造周期缩短。